Introduction
Acrylonitrile Butadiene Styrene (ABS) is a widely used thermoplastic polymer known for its excellent mechanical properties, impact resistance, and versatility. Composed of three monomers—acrylonitrile, butadiene, and styrene—ABS combines the strength and rigidity of acrylonitrile and styrene with the toughness of polybutadiene rubber. This unique composition makes ABS a preferred material for various industrial and consumer applications.
Properties of ABS
ABS plastic exhibits a range of desirable properties, including:
- High Impact Resistance: The butadiene component provides excellent toughness, making ABS suitable for durable products.
- Good Mechanical Strength: ABS offers rigidity and dimensional stability under load.
- Thermal Stability: It can withstand moderate temperatures, typically up to 80–100°C.
- Chemical Resistance: ABS resists acids, alkalis, and oils, though it is soluble in acetone and esters.
- Ease of Processing: ABS can be easily molded, extruded, or 3D printed, making it highly manufacturable.
- Surface Finish: It accepts paints, coatings, and electroplating well, enabling aesthetic versatility.
Applications of ABS
Due to its balanced properties, ABS is used in numerous industries:
- Automotive: Interior trim, dashboard components, and wheel covers.
- Electronics: Keyboard keys, computer housings, and consumer appliance casings.
- Toys: LEGO bricks and other durable toy parts.
- Construction: Pipes, fittings, and protective housings.
- 3D Printing: A popular filament due to its ease of use and post-processing flexibility.
Processing Methods
ABS can be processed using several techniques:
- Injection Molding: The most common method for mass-producing precise parts.
- Extrusion: Used for creating sheets, rods, and tubes.
- Blow Molding: For hollow objects like bottles and containers.
- 3D Printing (FDM): ABS filament is widely used in fused deposition modeling.
Environmental Considerations
While ABS is recyclable (classified under resin ID code #7), its petroleum-based origin raises sustainability concerns. Research into bio-based ABS and improved recycling methods is ongoing to reduce environmental impact.
Conclusion
ABS plastic remains a cornerstone material in manufacturing due to its versatility, durability, and ease of processing. As technology advances, innovations in ABS formulations and eco-friendly alternatives will further expand its applications while addressing environmental challenges.
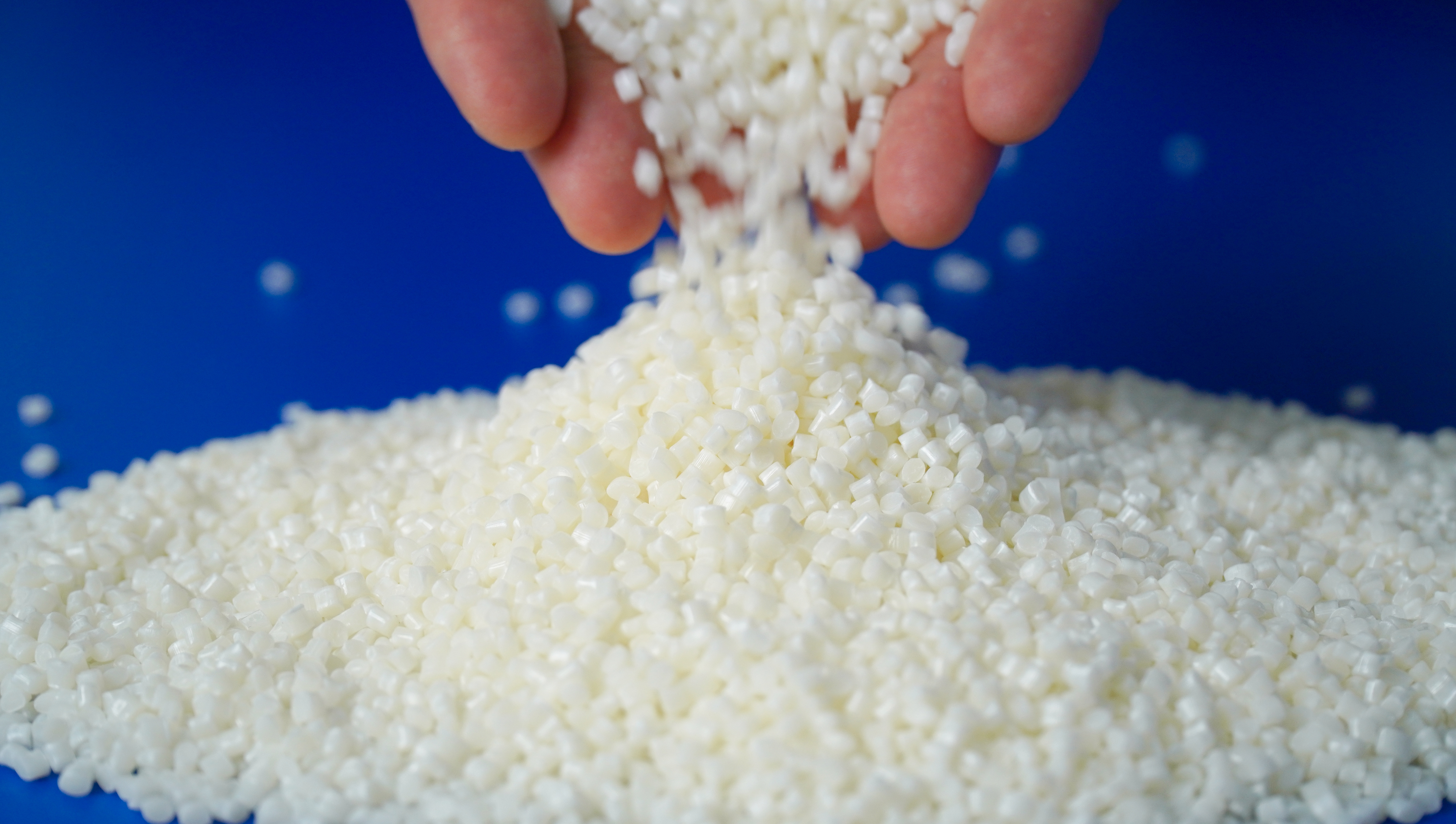
Post time: Apr-24-2025