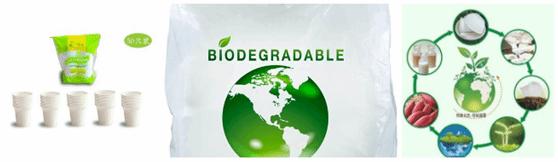
The perfect polymer—one that balances physical properties and environmental performance—doesn’t exist, but polybutylene adipate co-terephthalate (PBAT) comes closer than many.
Producers of synthetic polymers have for decades failed to stop their products from ending up in landfills and oceans, and they are now under pressure to take responsibility. Many are redoubling efforts to boost recycling to fend off critics. Other firms are trying to tackle the waste problem by investing in biodegradable biobased plastics such as polylactic acid (PLA) and polyhydroxyalkanoate (PHA), hoping natural degradation will mitigate at least some of the waste.
But both recycling and biopolymers face obstacles. Despite years of effort, the plastics recycling rate in the US, for instance, is still less than 10%. And biopolymers—often the products of fermentation—struggle to achieve the same performance and manufacturing scale of the established synthetic polymers they are meant to replace.
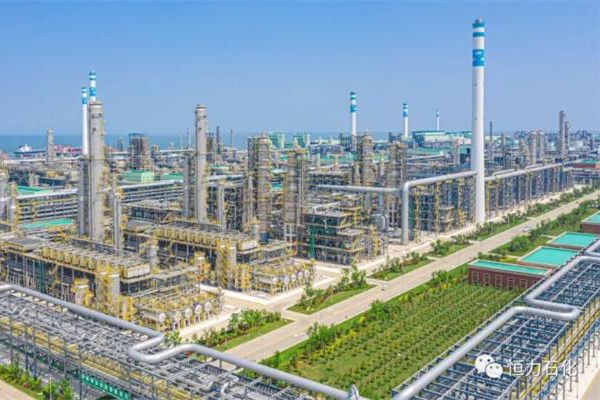
PBAT combines some of the beneficial attributes of synthetic and biobased polymers. It is derived from common petrochemicals—purified terephthalic acid (PTA), butanediol, and adipic acid—and yet it is biodegradable. As a synthetic polymer, it can readily be produced at large scale, and it has the physical properties needed to make flexible films that rival those from conventional plastics.
Chinese PTA maker Hengli. Details are unclear, and the company couldn’t be reached for comment. In media and financial disclosures, Hengli has variously said it is planning a 450,000 t plant or a 600,000 t plant for biodegradable plastics. But when describing the materials needed for the investment, the company names PTA, butanediol, and adipic acid.
The PBAT gold rush is biggest in China. The Chinese chemical distributor CHEMDO projects that Chinese PBAT production will rise to about 400,000 t in 2022 from 150,000 t in 2020.
Post time: Feb-14-2022